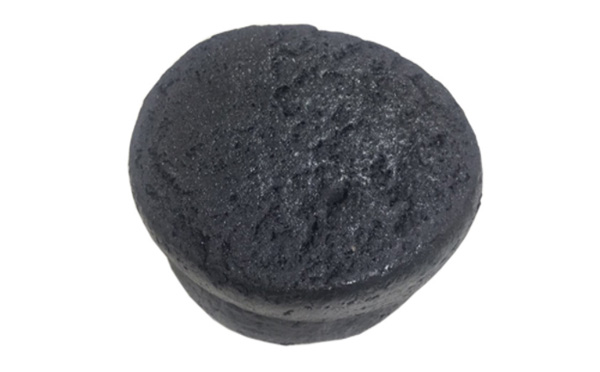
高炉用无水炮泥首先要具有良好的性能(出铁时间、铁口深度、扩径率、打泥压力、一次开孔率、稳定性等),配合炉前的操作,才能确保高炉生产的顺行和高产,增加高炉实现长寿的方法。无水炮泥在使用过程中会出现多个状况,如炮泥难打泥;泥炮压力低,炮泥无法推送至出铁口处;铁口难打开;铁水扩张太快;铁口喷溅;出铁时间短;铁口深度变短等等;
高炉炉前操作,影响无水炮泥的使用效果,如出现打泥难,泥炮压力低,炮泥无法推送到出铁口处,这些原因都需要操作人员的仔细控制,控制无水炮泥量的使用,查看高炉情况,严格对待每次高炉出铁,确保无水炮泥在高炉的使用,避免影响高炉的正常运行。
无水炮泥在使用过程中出现的多种问题,首先确保无水炮泥的质量,其次需要专业技术人员了解高炉的基本情况及炉前的操作情况,查找真正影响高炉无水炮泥使用的原因,合理的调整,来达到高炉的正常运行和高产。打泥也就是泥炮机将无水炮泥推送到出铁口的过程,无水炮泥打泥的控制是在推送无水炮泥时的操作,打泥速度的快慢、打泥量的多少,是否连续打泥,打泥压力高低实施的控制。
由于打泥压力受炉缸内“松弛”程度,以及炮泥硬度等影响较大,一般只作为炉缸工作情况信息反馈给高炉操作人员,不将打泥压力作为打泥操作控制内容。能够参与打泥操作控制的只有打泥过程是否连续和打泥速度,在这两项操作内容当中,唯有打泥过程是否连续的控制最为简单,并且也能够达到预期效果。
所谓打泥过程是否连续,就是是否在打泥过程中进行“人为的停顿”,如果在打泥过程中进行了“人为停顿”,那么该打泥方法就被称为“间断式打泥”也称“分阶段打泥”。通过长期对高炉铁口打泥操作的跟踪调查,认为“分阶段打泥”操作方法比较常用,并且对保持出铁口深度、维护“泥包”能够起到重要作用。
高炉炉前操作人员使用的“分阶段打泥”方法,是先打入铁口孔道体积 3~5倍数量的炮泥,随后大约间隔 1s 时间再打入少量的炮泥,虽然两次打泥间隔时间较少,但是按照“泥包”形成基本原理分析,认为该操作方法基本上是正确的,应该属于“间断式打泥”的范畴,其第二次打泥的作用就在于将炮泥压入铁水液面以下,对泥包起到巩固的作用,如果进一步提高认识,把两次打泥的间隔时间延长至 5~10s,效果可能会更好,当然这需要通过炮泥的实际凝固时间来探索确定。无水炮泥的打入方式及打泥量的控制,对高炉的正常顺行也有着重要的关联。无水炮泥是高炉出铁口必用耐火材料,任何操作都会影响高炉的冶炼。
泥包是高炉无水炮泥作用下的“产物”,它是高炉出铁口堵塞时用泥炮机沿出铁口通道打入高炉内部的炮泥,在炉墙部位形成一个“蘑菇状”块体,附着在高炉炉墙内侧出铁口周围,用于阻挡高炉出铁时铁水铁渣对炉墙部位的冲刷及侵蚀,无水炮泥形成的泥包分为原始泥包和新生成泥包。原始泥包是高炉建炉时,开炉以前由工人进入高炉内将炮泥堆砌建造,随着高炉冶炼矿石,原始泥包被熔渣冲刷、侵蚀,新的无水炮泥逐渐的打入,再形成新的泥包来保护高炉出铁口周围的炉墙。
无水炮泥形成的泥包在使用中需要通过打泥的控制来形成,铁口维护来讲“两次打泥”优于一次性打泥,“三次打泥”优于“两次打泥”,其原因仍然与泥包形成原理有关,结合泥包形成原理对“三次打泥”的优越性进行描述,可提高高炉铁口的安全性和可靠性。
高炉出铁口在打泥时,把第一次打入的泥包以及所形成的“结壳”整体向前推移,使第二次打入的炮泥沿着炉墙向四周扩散,当然在受到铁水致密度的影响后其向下扩散的幅度会明显小于其他方向,因此,只有当打泥量达到一定程度,“泥包”结壳达到一定面积,打泥压力达到一定程度后“泥包”才能够向下增长,第一次打泥量必须仍然按照铁口孔道实际深度体积的 3~5 倍的数量控制打泥,千万不能因为铁口过浅而打泥过多,停顿时间必须延长到最大限度,给“泥包”“结壳”和水分蒸发或者挥发份挥发留出足够时间,为了使铁口“泥包”牢固和稳扎稳打地把铁口深度恢复上去,其打泥停顿次数或者说打泥次数,可以增加到 4 次甚至 5 次,但总打泥量必须控制在铁口孔道实际深度体积的 8 倍以内,打泥过多或者“涨铁口”心切,往往适得其反。通过控制打泥速度和打泥方式,防止炮泥“打穿”,增加促使泥包形成。高炉无水炮泥形成的泥包对高炉有着重要的作用,不仅保护炉墙,还可抵抗熔渣的侵蚀,对高炉的顺行有着重要的作用。