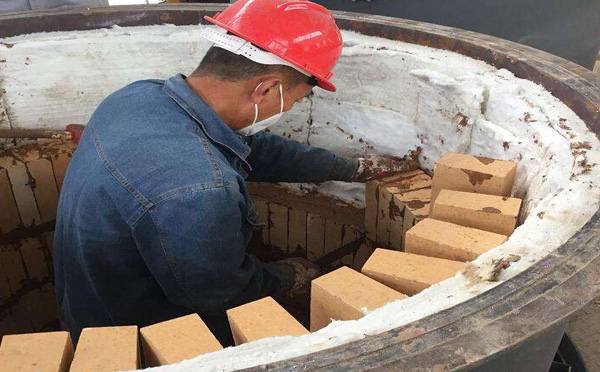
耐火砖在工业炉上的砌筑是离不开粘结剂耐火泥浆的,在砌筑耐火砖前应先将所用泥浆调配好,泥浆的最大粒度目数不应超过砌筑砖缝的20%,所用泥浆的理化性能指标要与砌筑的耐火砖品种材质匹配,最好是在购买耐火砖的时候就要求厂家配套相应的耐火泥浆,以避免混用。
在选用粘土耐火砖砌炉之前,厂方可在砌炉方案里核算出大概所需采购得数量,可减少不必要的浪费并且要注意砌筑灰缝应使用一级灰缝砌筑。
砌筑粘土砖时,如果自行配制粘土质耐火泥,则可取熟料:生料=70% : 30%.
熟料是硬质耐火粘土经高温煅烧而得,也可使用废砖,经磨碎后即可。生料就是轻质耐火粘土。
如果要计算耐火泥的各种组成,只要将已知所需耐火泥的重量,代入公式(1)公式(2)即可。
(1)熟料重量=耐火泥重量 x 70%
(2)生料重量=耐火泥重量 x 30%
当采用 T--3 标砖(230x114x65mm)进行砌筑时。应熟记下列数字:
1、 每块耐火粘土砖重3.7kg
2.、每吨耐火粘土砖约为270块
3.、砌筑每吨粘土砖约需耐火泥76kg
4、 砌筑每立方米砌体约需594块砖
5、 砌筑每立方米砌体约需2.2吨砖
一:耐火泥浆的调配要求
耐火泥浆调制的一般规定应根据砌体类别,通过试验确定泥浆的稠度和液体加入量,同时检查泥浆的砌筑性能(粘结时间)是否满足砌筑要求。泥浆的粘结时间视耐火制品的材质,外形尺寸的大小而定,宜为不大于2min为合适。不同泥浆选用的目数和稠度应根据砌体的类别按下表选定。

测定泥浆的稠度,应按现行的国家标准《耐火泥浆稠度实验方法》的规定进行。测定泥浆的粘结时间,应按现行的国家标准《耐火泥浆粘结时间实验方法》的规定进行。
调制泥浆的方法有水自然结合、化学结合两种方法现行工业炉砌筑中大多采用化学结合方法调配,里面掺入相应的促凝剂,其特点是凝结速度快,粘结强度高,在高温使用下不产生烧结后脆化的现象,而使用水结合的泥浆砌筑后,窑炉高温下水蒸发,泥浆砌体容易出现脆化现象导致砌体不牢固。另当天调配的耐火泥浆要在当天使用完。
二:耐火泥浆的使用量计算方法
在整个工业炉砌筑耐火砖用耐火泥的使用量上,一直没有一个很好的计量方法,这是因为工业炉的炉型不同,砌筑的砖型也不一样,有可能所砌筑的是异型耐火砖非标准耐火砖或者砌筑的部位不一样,炉墙、炉顶、炉底砌筑单块砖用耐火泥的使用量都是不一样的。目前在工业炉造价或预算中用耐火泥的使用量主要是以砌筑炉墙用标准型号耐火砖的使用量为参考。另还需参考砌筑灰缝,灰缝是计算一块标准耐火砖用耐火泥的基本参数,先要定位砌筑灰缝是采用I级灰缝<1mm、II级灰缝<2mm、III级灰缝<3mm。三类灰缝的那一类,一般砌筑粘土耐火砖或高铝耐火砖使用的是II级灰缝。
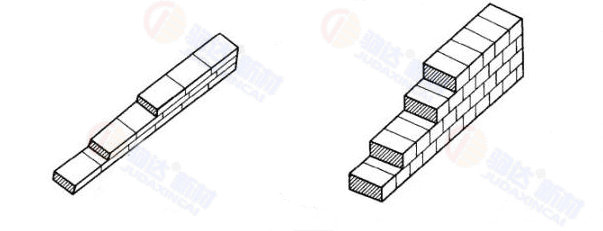
例如:砌筑工业炉的炉墙要计算所砌的1000块高铝耐火砖一共需要用多少耐火泥的计算方法需要先知道:A=砌筑灰缝(2mm)B=所砌筑砖型尺寸单层面积(T-3尺寸230*114*65)
C=所用耐火泥浆质量(高铝泥浆质量2300Kg/m³) D=每块砖所需泥浆用量。最终算出泥浆用量D=230*114*2*2500=0.13Kg(每块用量) 。那么得知1000块高铝耐火砖一共用量约在130Kg耐火泥浆。此计算方法为理论计算方法,实际使用量应大于理论数据的10%左右。
耐火泥又称火泥或接缝料(粉装物)。用作耐火制品砌体的砌缝材料。按材质可分为黏土质、高铝质、硅质和镁质耐火泥等。由耐火粉料、结合剂和外加剂组成。几乎所有的耐火原料都可以制成用来配制耐火泥所用的粉料。以耐火熟料粉加适量可塑黏土作结合剂和可塑剂而制成的称普通耐火泥,其常温强度较低,高温下形成陶瓷结合才具有较高强度。以水硬性、气硬性或热硬性结合材料作为结合剂的称化学结合耐火泥,在低于形成陶瓷结合温度之前即产生一定的化学反应而硬化。
耐火泥的粒度根据使用要求而异,其极限粒度一般小于1mm,有的小于0.5mm或更细。
选用耐火泥浆的材质,应考虑与砌体的耐火制品的材质一致。
耐火泥种类繁多,按化学特性分为酸性耐火材料、中性耐火材料和碱性耐火材料。此外,还有用于特殊场合的耐火泥。